Assembly Solutions
AEHH understands that increasing productivity is a priority for your company. Whether reducing cycle times, improving quality control, workplace ergonomics or simplifying your process, AEHH has solutions that will increase your bottom line. Choose your category below, to learn more about what solutions we can provide you.
Reactionless, Transducer Controlled Solutions
In recent years, eliminating torque reaction has become one of the most inquired topics among manufactures who use torque control tooling. AEHH understands your need and is ready to help with your application. When torque arms and reaction bars are not an acceptable option, the below solutions will deliver the performance that you are looking for.
Features of reactionless, transducer-controlled tools
Time Advantages
- One step process, eliminates the need to verify torque with a hand wrench or other audit method
- Faster rpms than continuous drive tools
- Simple to program
Ergonomic Advantages
- Pulse mode results in little to no torque reaction
- Battery Platform in select models eliminates tripping hazards and provides ultimate maneuverability
- Reduced noise compared to impact wrench
- Less vibration than impact wrenches
Quality Advantages
- Transducer controlled for optimal torque control
- Angle control and monitoring in select models
- Data collection and line integration
Benefits to Your Process
- Decreased Risk of Injury
- Improved Quality Control
- Reduced Energy Consumption
- Reduced Maintenance Costs
Our Reactionless, Transducer-Controlled Tool Vendors
AEHH is fortunate to have relationships with multiple vendors who fall into this category. Select one of the companies below by their logo or scroll below to learn about the features that could prove to be the key requirement in your application.

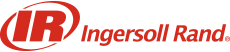
AIMCO’s brushless Magnetostrictive Torque Transducer consists of an Anvil and a pair of sensor coils. Without contacting the Anvil, the sensor coil detects load to the Anvil (non-contact). The grooves in the Anvil are provided at a 45 degree angle in one region. When torque is applied to the Anvil, tensile stress appears on the region and magnet permeability increases. These permeability changes are detected, respectively transformed to the voltage change (proportional to applied torque) and converted to torque signals to control the tool.
Their inline series features torque ranges of 5NM – 600NMand their pistol tools offer 6.8NM – 400NM. For data collection and line integration, pair these tools with a touch screen controller equipped with your plants protocol.
Features
- The UA-MC features patented Auto Relief Technology providing additional control to the application of the torque during the pulsing event.
- Provides increased power under load with the 10-blade triple-chamber motor and patented double-blade with rollers pulse mechanism
Productivity
- High speed rundown reduces fastening time
- One hand operation frees the other for productive use
- Ergonomic benefits reduce fatigue and increase productivity
- Quick and easy forward and reverse operation with single-hand reverse lever
Ergonomics
- Virtually no reaction impulse during and after fastening rundown
- Fast rundown reduces operator exposure
- Low vibration and sound levels due to absence of metal-to-metal contact
- The external solenoid valve increases power-to-weight ratios by 20%
- Anti-vibration jacket handle provides comfortable operator handling
- Exhaust silencer with combined one-piece air inlet bushing
-
- Quick and easy forward and reverse operation with single-hand reverse lever
Reliability
- Magnetostrictive Transducer provides increased durability with low size and weight
- No mechanical clutch or hard part engagement for low maintenance and longer life
- Extended socket and extension life
Quality
- All modes work with any UEC Series controller that will connect to a wide range of network protocols
- Built-in torque adjuster matches each application for required torque and fastening time
- Extremely accurate on properly designed joints
- Excellent clamp force repeatability
Reducing the torque reaction in your fastening process doesn't have to be complicated. Control and ergonomics not compromise - that is what the QX ETS is all about. The QX ETS offers all the capabilities found in the QX Series™ platform, without the torque reaction.
SIMPLE SETUP: In addition to standard direct drive mode, each tool configuration can be independently programmed to utilize one of the three available single-parameter ETS modes, simplifying setup.
ERGONOMIC MODE: Lowest energy pulses; ideal for hard joints or when arm, wrist or tool angles are most difficult.
PERFORMANCE MODE: Medium energy pulses; is the best all-purpose mode.
PRODUCTIVITY MODE: Highest energy pulses, is the fastest mode. Ideal for soft joints or when high production rates are required.
- Ergonomically enhanced motor control algorithm significantly reduces the average force experienced by the operator during the tightening process
- Red tool highlights provide clear indication of ETS tool identity vs standard QX tool
- Continuously flashing blue light above keypad provides operator assurance that ETS is ACTIVE
- All the capability of the QX platform, without the torque reaction from 1.6 NM – 80 NM
- Common software and battery platform for simple integration
- QXN, QXC and QXX versions available in pistol grip, low torque angle and high torque angle
- Onboard ‘pulse’ counter supports proper optimization and application of ETS tools on ideal applications (10 pulses or less per cycle)
For more information on transducer-controlled pulse solutions or to schedule a demonstration, please contact us today.
AIMCO HT Series and IR Qx Multiplier
When controlling turn torque on large diameter bolts, it is very challenging to find tools that are designed to do this task. AIMCO’s HT Series was specially designed for high volume applications with high torque requirements. This transducer-controlled series was designed to control up to 15,000 NM of torque, making AIMCO the industry leader in transducer controlled high torque tooling. IR’s Qx Multiplier gives a great battery-operated solution in both Pistol and Right-Angle Configurations.
Features of High Torque Control Tools
- One step process, eliminates the need to verify torque with a hand wrench or other audit method
- Simple to program
- Light Weight when carrying around work site
- NO MULTIPLIERS - AIMCO's HT Series was designed to handle the workload during high cycle use.
- Battery Platform in select models eliminiates tripping hazards and provides ultimate maneuverability
- Custom reaction bars, allow for the perfect reaction plan
- Dual level start protects operator from accidental start up.
- Transducer and Angle Controlled for optimum results
- Data collection and line integration
Benefits to Your Process
- Increase Time Savings
- Reduce Injuries
- Improve Quality Control
Our Vendors for Transducer-Controlled High Torque Tools
AEHH is fortunate to have relationships with multiple vendors who fall into this category. Each company have features that could prove to be the key requirement in your application. Select on of the below icons to see that manufactures solution, or simply scroll down.

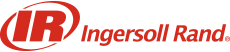
Critical bolting demands tools that will deliver high torque with superior performance. The HT Series from AcraDyne combines these features in an electric, high-torque bolting tool that beats the competition in accuracy, speed and safety.
When combined with AcraDyne’s controller, customers have a high-torque critical bolting system that can handle the toughest and most important bolting jobs.
- One of the most accurate high-torque tools in the world today
- Up to 100 times faster than hydraulic tools
- 50 Nm - 15,000 Nm
- Ergonomic, robust design with five handle configurations, including duel trigger to eliminate accidental start up.
- Over 300 models to choose from
- Built-in integral transducer for optimal monitoring and control
- The world's ONLY traceable system at the square drive
- Data retrieval
- Designed and MADE IN THE USA
The innovative QX Series Cordless Torque Multiplier will reduce your bolting time and cost, while ensuring repeatable accuracy for all torque-critical joints. Designed with a premium Norbar™ gearbox and an efficient, time-tested closed-loop transducer, the Torque Multiplier is world-class in quality, control and programmable configurations to maximize your productivity.
FEATURES
- Closed-loop transducer delivers a torque accuracy of +/- 5% from
- 40NM – 2000 NM
- Integrated gearbox provides premium quality and accuracy
- Brushless Motor offers maximum durability
- Multi-function display module with cycle status alert and audible alarm offers instant feedback and easy setup
- 360° adjustable handle, with 6 mm threaded port for eye hooks or other tethering points, provides operator comfort, flexibility and safety options
- Standard or custom reaction arms available
- Optional wireless communication for process control with I/O and data collections (USB connection standard)
- Ingersoll Rand’s ICS software provides operators the ability to access and program basic fastening strategies, as well as more advanced options to adapt to the most complicated bolting applications
- Class 1 Division 2 Haz Tool option available
For more information on AEHH's solutions to high torque application or to schedule a demonstration, please contact us today.
Hydraulic Tensioning Solutions
Securing large thread nuts doesn’t have to be a dangerous or time-consuming task when using Boltight tensioners. By hydraulically stretching the stud, high preloads are controlled quickly and easily. With many different products to fit common applications, we will help you find the style tensioner that best fits your application. For tight spaces in the wind industry, large press columns or countless other applications, you can rely on Boltight to overcome any tensioning challenges you may be facing.
Features of Boltight Tensioning Solutions
- Simple set up
- Fast and simultaneous loading of studs for equal clamp load
- Brings joints under full load fast and safe
- Select Models feature an auto relief valve to prevent overstroke
- Tensioning Accuracy - control your preloads to within 10%, much more repeatable than with turn torque methods
- Intelligent Electric Pump allows for tension data to be recorded with date and time stamped.
Benefits to Your Process vs Hand Tightening Methods
- Time Savings to Install and Remove
- Improved Quality Control
- Reduced Risk of Injury
Click Here to learn more about Boltight on our Nord Lock Group Tab or contact us to discuss your tensioning application.
Lean Manufacturing with Custom Shadow Boards
Disorganized workspace and critical assembly tasks with overwhelming hardware both present challenges to manufacturers. A cluttered workspace can lead to bottlenecks and time loss, when tools and other equipment is difficult to find. Assembly tasks that have critical steps or large quantities of hardware can lead to missed screws, nuts, bolts and other components. OSAAP Shadow Boards provides the solution to both challenges with their custom shadow boards. Custom designed shadow boards allow you to keep track of your tools and process with a clean and simple process. 6S Lean has become a vital practice for manufactures and service industries alike, read more below about how OSAAP Shadow Boards can improve your workflow process.
Features of OSAAP Shadow Boards
- Know where all your tools are and easily access them
- Portable light station allows you to design boards without tooling leaving your building
- OSAAP’s in house design engineer will organize the board to your request at no charge.
- Convert our files to DXF for in house milling and manufacturing.
- Protect your tools from unnecessary wear and tare
- Protect your tooling during transport and on the job site
- Kitting Projects - boards offer assurance that all components were assembled in your process. Ask about smart kitting for line integration!
- ESD compliant boards
- Layout and design board to your requirements.
Benefits to Your Process
- Increase Time Savings
- Reduce Injuries
- Improve Quality Control
Contact us today to learn more about OSAAP Shadow Boards and start designing a custom shadow board for your application!

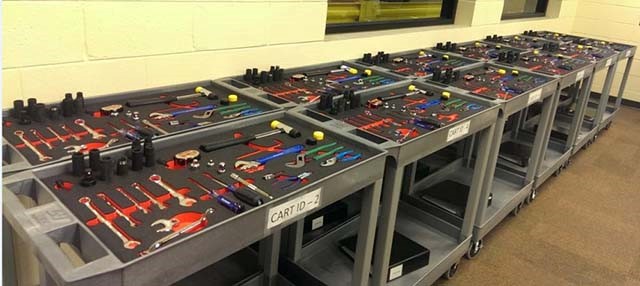
War on Hammers
Despite being inherently dangerous, many manufactures must rely on hammers to install products like caps, pins, bearings, bushings and many other parts of all geometry. Hydraulics can cost a fortune and most of the time create a bottleneck that disrupts your workflow, making swinging hammers a necessary evil. AEHH has a solution by using low vibration air tools and custom designed end tooling. Honsa Ergonomic Technologies have realized this market and reacted by adding in house design, machining and heat-treating capabilities. Small plastic parts? Large Steel Pins? No Problem! We have solutions for the most delicate jobs to parts that weigh over 100 lbs.
Contact us today to join the War on Hammers!
Features of Pneumatic Driving Systems
Time Advantages
- Complete task in 3 seconds or less
- Tool never slows down; operators slow down as fatigue sets in
- Quick change system allows for multiple punches to be used with one tool
Ergonomic Advantages
- Eliminate injuries like Repetitive Motion Strains to the hand, wrist, arm, back and shoulder, CTS, Hand Arm Vibration Syndrome, Tendonitis and Hernia
- Protect workers from vibration when using Honsa Ergonomic Technology's patented system
Quality Advantages
- Control amount of air to prevent overdriving
- Pair with an air qualifier to count cycles
- Smart Punches verify that your part was driven to complete
Benefits of Eliminating Hammers
- Increase Time Savings
- Reduce Injuries
Before and After
AEHH has been blessed to be allowed to document a small handful of jobs that we have completed over the years. The below gives an example of how broad the War on Hammers is and how creativity is often applied when implementing this innovative technology.
Die Insert Installation
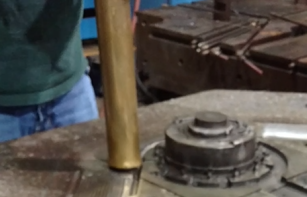
When installing inserts into die cavities, using brass cylinders is a very common method but often can result in hand, arm and back injury. AEHH has pioneered a pneumatic driving solution that will help keep your workers from experiencing these injuries that result from the repetitive process of die repair.
Bushing Installation
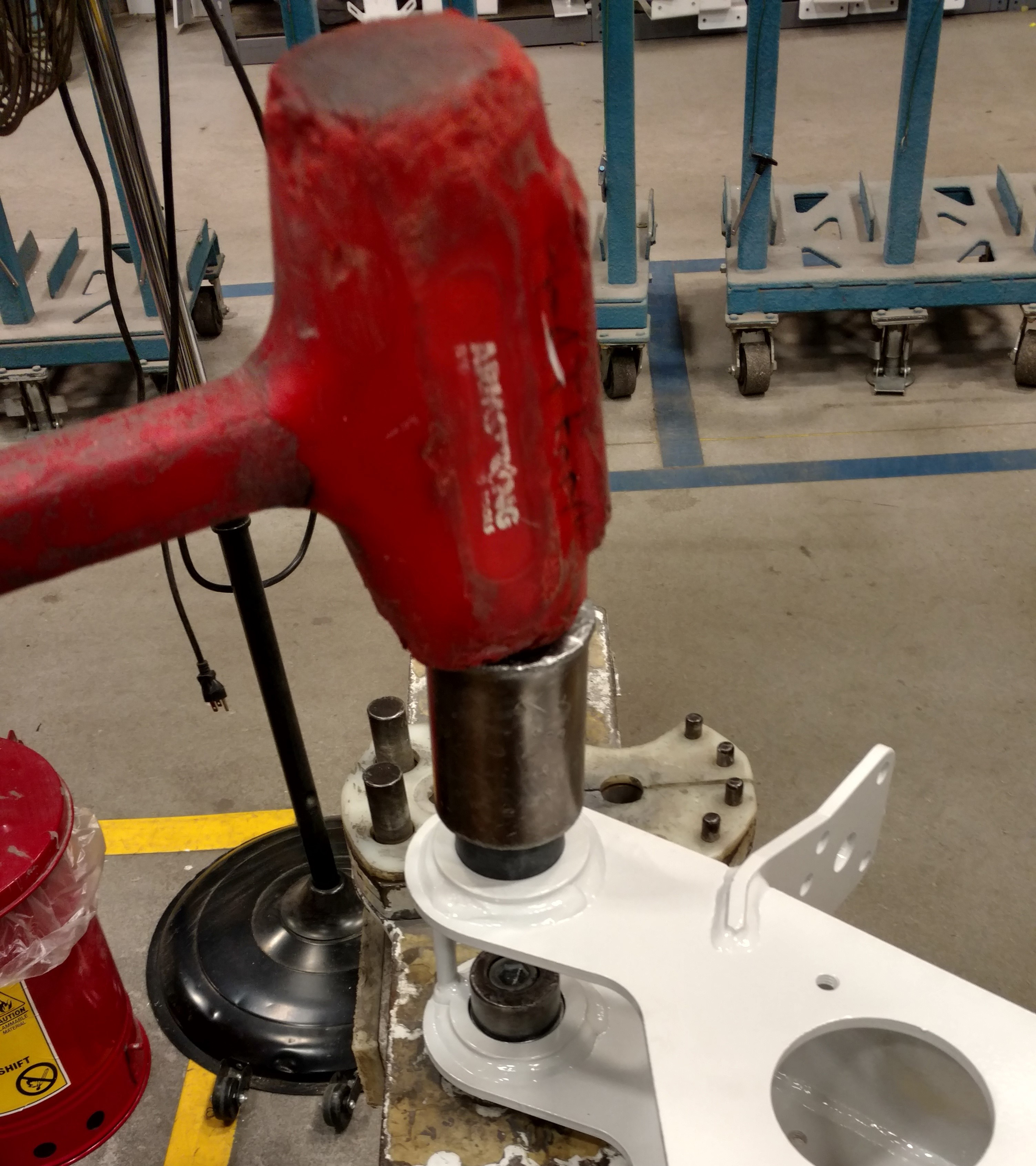
Shown above, a heavy construction equipment manufacture experienced great benefit from using the Honsa low vibration air tool with a custom driver by eliminating repetitive motion injuries and improving the overall cycle time vs using a hand and hammer installation method.
End Cap Installation
When required to install an end cap each minute, this fireplace manufacture turned to AEHH to provide a solution that keeps their operator from swinging a hammer. The square geometry allows the operator to quickly locate and align the cap without slowing down their cycle time.
Cam Bearing Removal
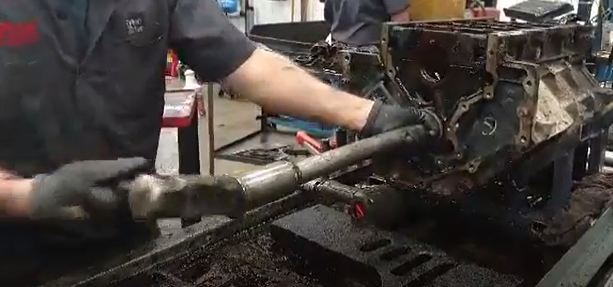
When removing over hundreds of cam bearings daily, this engine remanufacture uses Honsa’s low vibration air hammer with a custom punch in replacement their manual hand and hammer method. Using the Honsa’s tool protects the operator’s hands from becoming tingling or numb due to vibration and shock caused by the air hammer.
Die Insert Removal
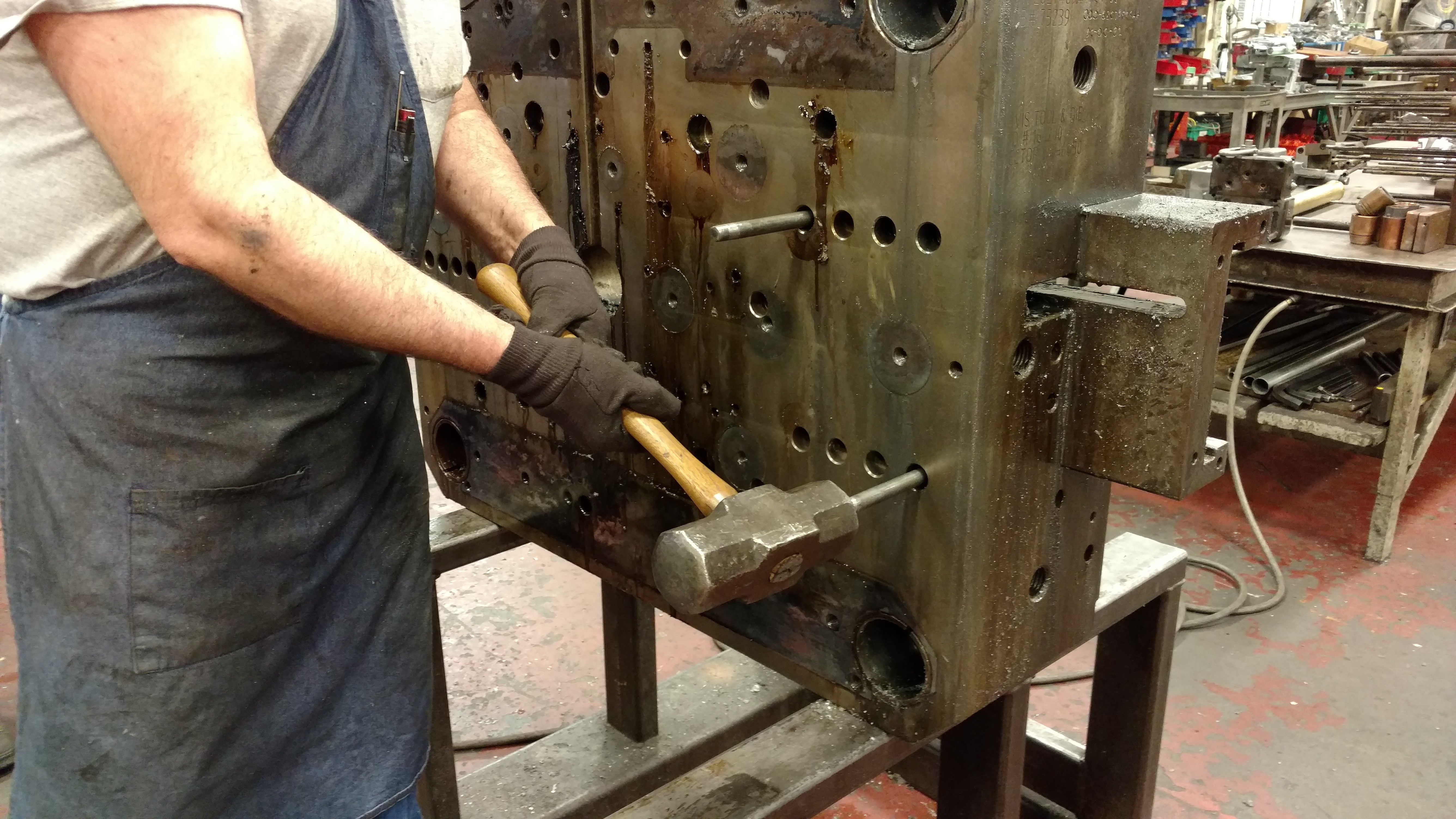
The above application improved the safety and control during the removal an insert for a midwestern die cast manufacture. When swinging the hammer, it takes 10 to 20 seconds to drive each rod but when using the Honsa solution it takes 3-5 seconds per rod.
Ready to join the War on Hammers? Contact us today to learn more about pneumatic driving systems or schedule an onsite demonstration.